The Rise of Rapid Manufacturing Companies: Transforming the Future of Production
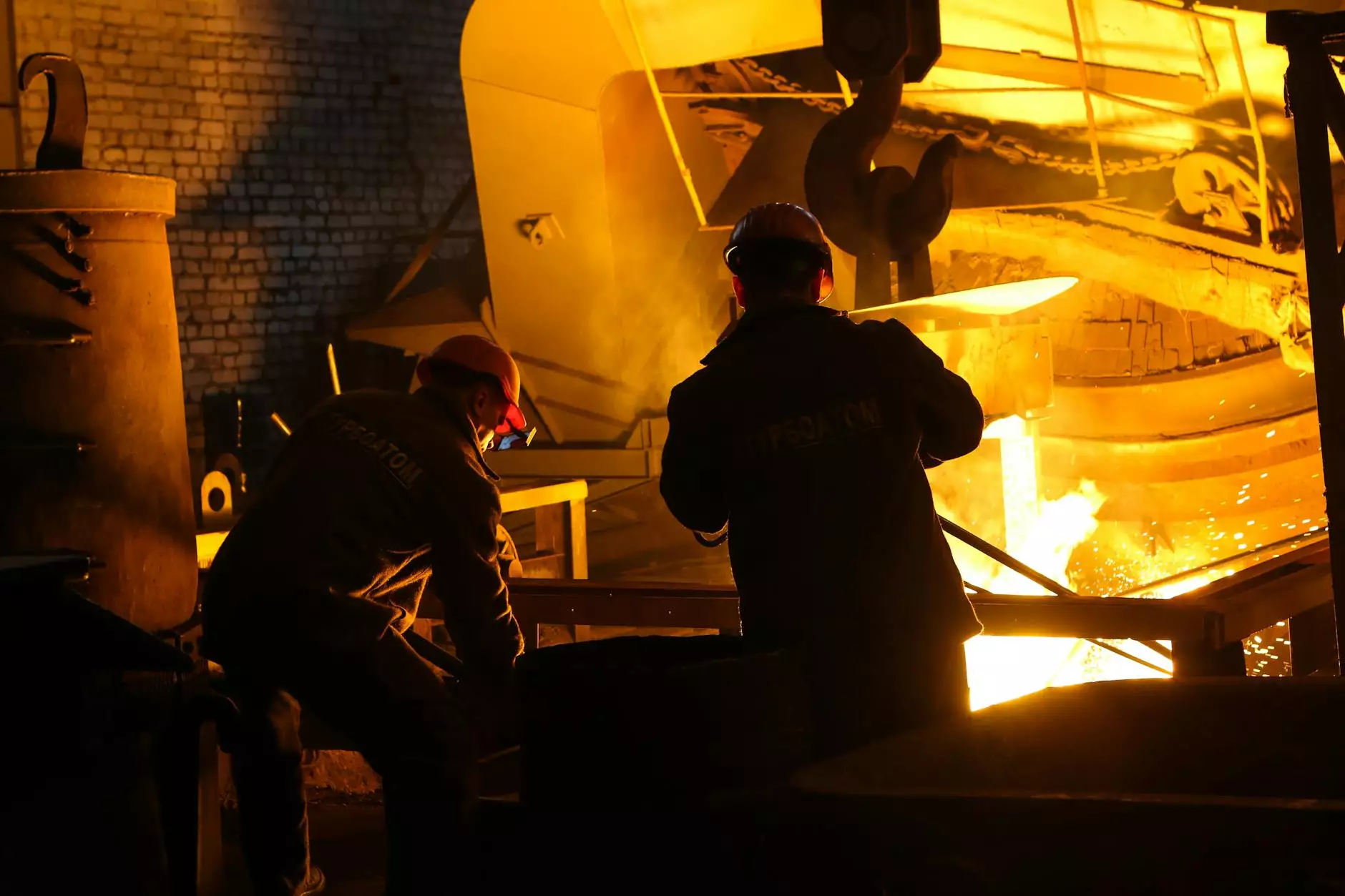
In today’s fast-paced world, where demand for products continues to escalate, the manufacturing sector finds itself at a crucial juncture. Rapid manufacturing companies have emerged as a key player in this landscape, leveraging advanced technologies to offer innovative solutions that meet the needs of modern consumers and businesses alike. This article delves deeply into the essential attributes of rapid manufacturing and its transformative effects on industries, particularly in the realm of metal fabrication.
Understanding Rapid Manufacturing
Rapid manufacturing refers to the process of producing parts and products quickly and efficiently using additive manufacturing techniques, such as 3D printing, alongside traditional subtractive methods. This methodology allows for quicker production cycles, reduced material waste, and increased design flexibility.
Key Features of Rapid Manufacturing
- Speed: The defining characteristic of rapid manufacturing is its ability to produce items at a much faster rate compared to conventional methods. Traditional manufacturing can take weeks or even months to develop prototypes, while rapid techniques can achieve this in days or hours.
- Customization: Rapid manufacturing allows for high levels of customization and personalization of products, catering to specific customer requirements without the need for extensive lead times.
- Efficiency: Utilizing techniques such as 3D printing not only speeds up the production process but also reduces waste, leading to more sustainable practices.
- Cost-Effectiveness: While initial setup costs for technologies may be higher, rapid manufacturing can lower overall production costs by minimizing material waste and shortening lead times.
The Impact of Rapid Manufacturing on Metal Fabrication
In the realm of metal fabrication, the influence of rapid manufacturing companies is profound. Traditionally, metalworking required multiple complex processes, each contributing to longer production times. With the integration of rapid manufacturing, companies in the metal fabrication sector are now able to innovate profoundly.
Streamlining Processes
Rapid manufacturing technologies enable metal fabricators to streamline processes such as:
- Prototyping: Rapid manufacturing significantly shortens prototyping phases, allowing metal fabricators to test designs quickly and iterate on them based on feedback.
- Tooling: The development of tooling, which is often time-consuming and expensive, is simplified, offering fabricators the ability to create tooling directly from digital models.
- Production Runs: Short-run production is facilitated, making it easier to deliver customized orders for clients with minimal delay.
Technological Advances Driving Rapid Manufacturing
The surge of rapid manufacturing companies can be largely attributed to remarkable technological advancements. Below are some key technologies reshaping the industry:
1. 3D Printing Technology
3D printing, or additive manufacturing, allows for the layered creation of objects directly from a computer-aided design (CAD) file. This method is particularly advantageous for fabricating complex geometries that would otherwise be impossible with traditional techniques. Metal 3D printing, specifically, enables the production of intricate parts with high strength-to-weight ratios, essential in aerospace and automotive applications.
2. Digital Manufacturing and Industry 4.0
The concept of Industry 4.0 encompasses the digitalization of manufacturing processes. The integration of IoT (Internet of Things), big data, and AI technologies facilitate real-time monitoring, predictive maintenance, and enhanced operational efficiency for rapid manufacturing companies. By utilizing these technologies, companies can refine their production processes, ensuring quality control and reducing downtime.
3. Computer Numerical Control (CNC) Machining
While CNC machining is a traditional method, its synergy with rapid manufacturing technologies enhances precision and efficiency. By automating the machining process, companies can manufacture parts with high accuracy while drastically reducing the time taken to perform tasks.
The Advantages of Partnering with Rapid Manufacturing Companies
For businesses, aligning with rapid manufacturing companies offers numerous benefits that can significantly impact their competitiveness and operational effectiveness:
1. Faster Time to Market
In many industries, being first to market can provide a crucial advantage. Rapid manufacturing companies can expedite the entire production cycle, allowing businesses to launch products faster than their competitors. This is particularly vital in technology-driven markets where consumer preferences constantly evolve.
2. Reduced Costs
By embracing rapid manufacturing, businesses can minimize several costs, including:
- Material Costs: Reduced waste and optimized usage of materials lead to significant savings.
- Labor Costs: Automation and digitization result in decreased labor inputs necessary for production.
- Inventory Costs: Rapid manufacturing methodologies eliminate the need for extensive inventory, as products can be made on-demand.
3. Enhanced Product Quality
With the precision afforded by rapid manufacturing technologies, businesses enjoy improved product quality. The ability to quickly iterate designs based on testing results leads to more reliable and better-performing products hitting the market.
4. Greater Flexibility and Scalability
As businesses grow and shift focus, rapid manufacturing companies can adapt to new requirements quickly. Whether it's scaling up production for a popular item or pivoting towards the development of a new product line, these companies provide the necessary flexibility to accommodate changing business dynamics.
Challenges Facing Rapid Manufacturing Companies
While the advantages are compelling, rapid manufacturing companies are not without challenges. Understanding these hurdles is essential for businesses looking to partner with these innovators:
1. Material Limitations
Although technologies like metal 3D printing are improving, material selection is still limited compared to traditional manufacturing processes. Companies must carefully evaluate available materials to ensure they meet the quality and performance needed.
2. Initial Investment Cost
The initial cost of adopting advanced manufacturing technologies can be high. Businesses must weigh these upfront investments against the potential long-term savings and efficiency gains.
3. Training and Skill Development
Rapid manufacturing introduces new technologies that require specialized knowledge and skills. Investing in employee training programs is essential to harness the full potential of these advancements.
Conclusion: The Future of Rapid Manufacturing Companies
The trajectory of rapid manufacturing companies is set for tremendous growth as industries seek to optimize production processes and enhance product offerings. As innovations in technology continue to evolve, the landscape of manufacturing will become increasingly dynamic and adaptive. Businesses that embrace these advancements will not only improve their operational efficiencies but also position themselves favorably within their respective markets.
At Deep Mould, we understand the importance of staying at the forefront of manufacturing innovation. With a focus on metal fabricators and the rapidly transforming environment, we are committed to providing high-quality solutions that meet the demands of our customers in the modern marketplace.